Contents
In short, it means being proactive rather than reactive.
What does preventive maintenance actually achieve? It increases equipment productivity, efficiency and safety.
With HelloHouston, you can :
- Increase machine availability by 20%.
- Reduce administrative tasks by 50%, allowing teams to focus on added value
In this article, we'll explain what preventive maintenance is, and how HelloHouston makes it easier to put it into practice, thanks to its features and support.
1. What is preventive maintenance?
Definition
Preventive maintenance encompasses all the routine maintenance work to be carried out on equipment, in order to anticipate breakdowns and failures.
In short, it schedules: follow-ups, inspections, adjustments and repairs. And all this to ensure that equipment is in excellent working order.
Maintenance levels
Preventive maintenance goes far beyond a simple maintenance plan. At HelloHouston, we aim to make it a corporate culture, involving all stakeholders in the maintenance of production machines.
This requires a skilled workforce.
In France, Afnor standard X 60-010 (1994) provides a framework for this proactive approach. In Europe, the standard is EN 13306:2001.
These standards define several levels of maintenance (1 to 5) to preserve equipment, each requiring specific qualifications. This hierarchy applies to both preventive and corrective maintenance.
Here is a summary table of the 5 maintenance levels:
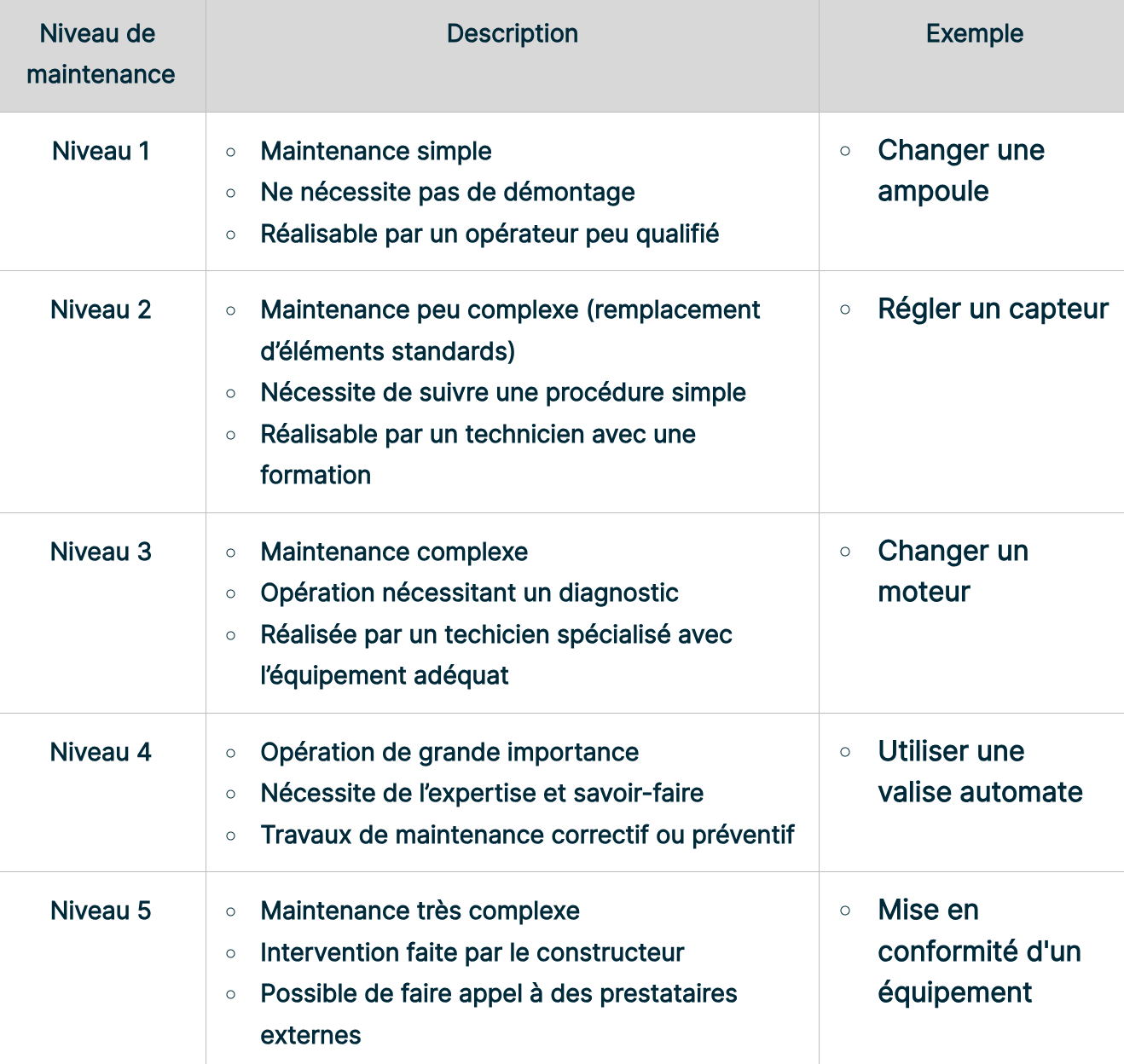
Initially, the aim of these levels is to involve everyone in the maintenance process, but also to free up technicians' time so that they can concentrate solely on truly technical tasks.
The second point is that by involving your operators more in the maintenance of their machines and developing their skills, they will be better prepared to react effectively in the event of a problem.
Preventive maintenance objectives
Preventive maintenance serves six main purposes:
Avoid unexpected breakdowns,
Increase equipment efficiency and longevity
Reduce maintenance costs
Improving equipment reliability
Improving operational efficiency
Easy to plan and manage operations
What's the difference between preventive and corrective/reactive maintenance?
Before going any further, let's clarify the difference between preventive and corrective maintenance:
- Preventive maintenance: Prevents breakdowns and malfunctions.
- Corrective maintenance: Responds to incidents by replacing worn parts or correcting bugs or programming errors.
The preventive approach anticipates, while the corrective approach repairs after the fact.
2- Types of preventive maintenance
Systematic maintenance
Systematic maintenance is like a regular check-up to ensure that machines are running smoothly. It is based on a schedule or on equipment usage (number of hours of use), regardless of the condition of the equipment.
With HelloHouston, you can set automatic reminders to let you know when it's time to check the equipment.
Example: Maintenance of air conditioning units in an office building every 3 months.
Conditional maintenance
This method uses data from sensors and monitoring systems to assess the condition of machines and determine when maintenance is required. The aim is to intervene only when required, thus preventing breakdowns while optimizing costs and equipment life.
Conditional maintenance can be compared to the oil sight glass on your car.
Example: Engine maintenance in a production plant when the oil level is low.
Predictive maintenance
Predictive maintenance is like meteorology. Instead of anticipating the weather, you anticipate when a machine needs maintenance.
You analyze real-time data sent by sensors installed on equipment and observe the evolution of degradation.
You want to be alerted when a piece of equipment is deteriorating. This is achieved by setting degradation thresholds that must not be exceeded. Real-time monitoring shows whether the equipment is deteriorating more or less rapidly.
Example: Turbine maintenance in a power plant. When sensors alert us to abnormal vibrations, an intervention is triggered.
3- The benefits of preventive maintenance?
Reduce breakdowns and production stoppages
Preventive maintenance enables problems to be detected before they cause breakdowns.
Increased equipment service life
Regular maintenance helps preserve machine components. This prolongs their service life and machine reliability.
Improving worker safety
Maintenance minimizes the risk of failure. It's like elevator safety devices. Checked regularly and well maintained, they offer better protection for your employees.
Optimizing maintenance costs
Poorly maintained equipment often breaks down and can cease to function. Preventing these major failures minimizes repair and replacement costs, as well as indirect costs.
Now that you understand the importance of preventive maintenance, find out how tools like HelloHouston can help.
4- What tools are used for preventive maintenance?
For effective preventive maintenance, an Excel sheet is not enough. Several documents are necessary, but they are often difficult for technicians to interpret, making the search for information complex.
Simplify maintenance management with an efficient CMMS.
HelloHouston manages preventive maintenance much better than a simple Excel spreadsheet. You can add all the information you need on equipment, spare parts and human resources.
- Data is hierarchically organized in a detailed tree structure. Exploiting this information is easy thanks to its many functions, including :
- Stock management and purchasing: spare parts are traceable (from purchase to use). Equipment condition can also be checked.
- Automated alerts: alerts can be automated to let you know when action needs to be taken.
- Request and incident management: alerts are sent in the event of requests or incidents. You can easily document and track every problem and request.
- Performance monitoring: HelloHouston lets you create tracking dashboards to help you achieve your objectives.
- Equipment management and tracking: equipment status can be tracked by consulting the maintenance history.
With HelloHouston, you have an overview of the availability and specialization of your technicians. This facilitates the coordination and planning of interventions.
Data analysis
.png)
IoT data arrives continuously. HelloHouston receives and sorts it for you. After analysis, you can view machine status and maintenance costs on the maintenance dashboard.
Thanks to KPIs, these analysis reports are a real beacon for improving operational efficiency.
5- How to set up a 5-step preventive maintenance plan?
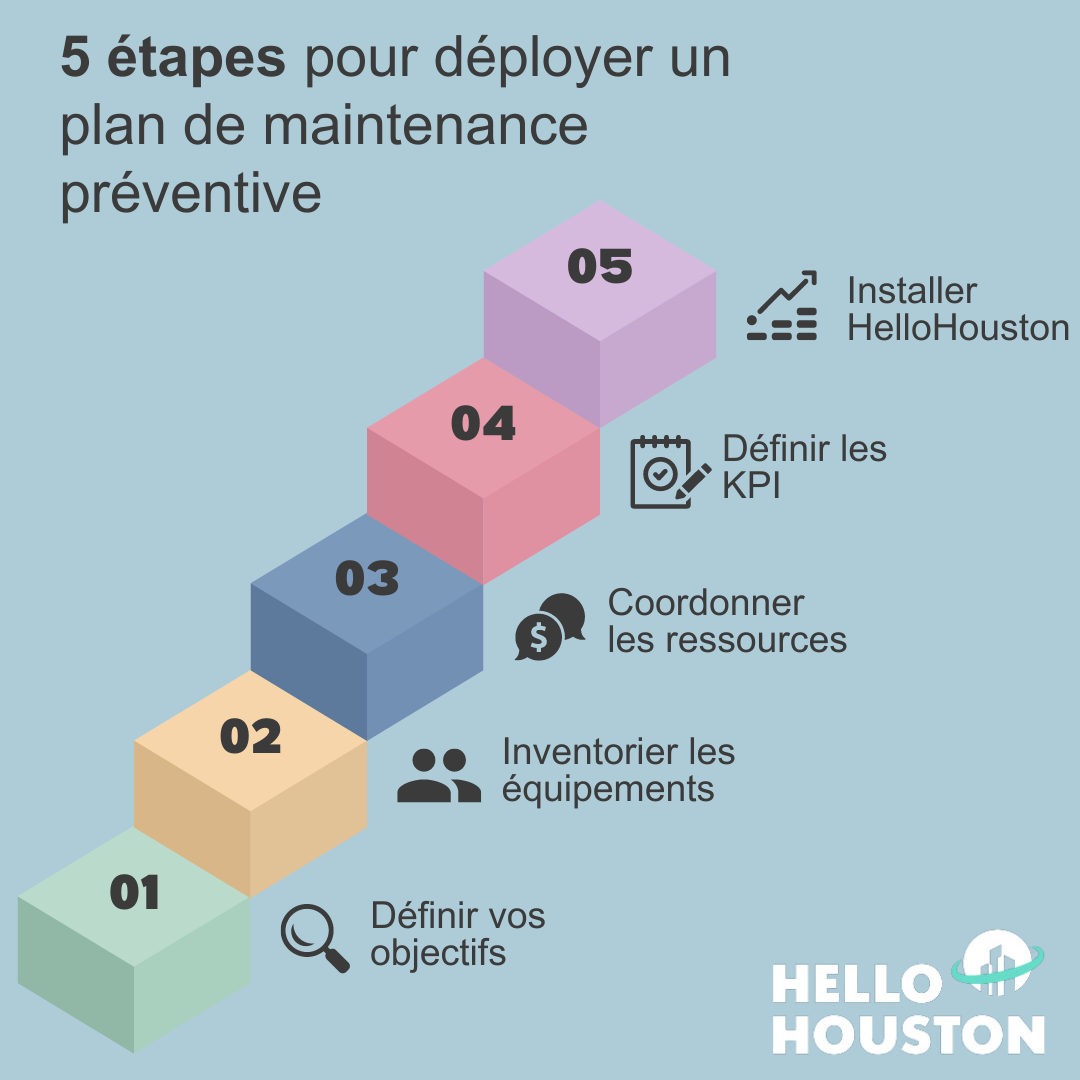
Now that we've understood what preventive maintenance is, here are the steps to help you implement it quickly and easily in your workshop:
1. Define your goals
Identify what you want to achieve with preventive maintenance.
Perform a Pareto analysis of the most critical equipment.
Use Noiret's Abacus to get you started.
2. Inventory equipment and analyze failure history:
List all equipment with its current condition, age and frequency of use.
Analyze breakdowns to identify the frequency of maintenance interventions.
Example:
Pump: monthly seal inspection, filter replacement every six months.
Motor: lubrication quarterly, electrical connections checked annually.
3. Coordinate priorities and resources according to the production schedule:
Ensure that resources (personnel, parts, tools) are available to maintain priority equipment.
Improve communication with the production department.
4. Define KPIs :
Manage your performance to meet maintenance plan targets.
Define key performance indicators (KPIs) such as MTTR, MTBF, and preventive maintenance rate.
Remember, you can only improve what you measure.
5. Using HelloHouston :
Implement our software to plan, monitor and analyze maintenance activities.
Facilitate access to documentation for technicians.