Contents
Managing equipment maintenance is a real headache for many manufacturers. Unexpected breakdowns, high repair costs, and the difficulty of predicting when and how to intervene can cause costly and even stressful downtime.
Preventive maintenance offers a solution by reducing maintenance costs and limiting breakdowns. The aim is to strike an optimum balance between the timing and frequency of maintenance.
This is precisely why condition-based maintenance was introduced.
This type of maintenance, sometimes confused with predictive maintenance, is essential for optimizing interventions. In this article, we explain the concept, its advantages and how it works, and show how HelloHouston can help you.
Conditional or systematic maintenance?
Take a minute and imagine two plants: one performs systematic maintenance according to a fixed schedule, while the other uses condition-based maintenance. In the first plant, technicians intervene regularly, often unnecessarily. In the second, interventions are carried out when necessary and based on actual data.
What's best for you? Not always obvious, and there are nuances to consider. Let me explain.
Every machine has different preventive maintenance needs, to prevent unplanned downtime and failures. That's why there are several techniques/types of maintenance you can use. The ideal method depends on the criticality and type of equipment to be maintained.
Systematic maintenance :
Based on manufacturers' recommendations and historical breakdowns, this method involves periodic rounds without taking into account the actual state of the assets. It is planned and parameterized in the HelloHouston CMMS, enabling technicians to organize their day via a calendar.
Conditional maintenance
It enables equipment to be monitored in real time, and action to be taken only when necessary. By configuring and connecting sensors, you can be alerted when thresholds are reached, facilitating team organization.
To make sure you understand the difference, here's an example:
Brake inspection: Every 15,000 km (systematic maintenance)
Brake inspection: Based on brake pad wear, measured by a thickness sensor (conditional maintenance).
Conditonnal maintenance measurement tools
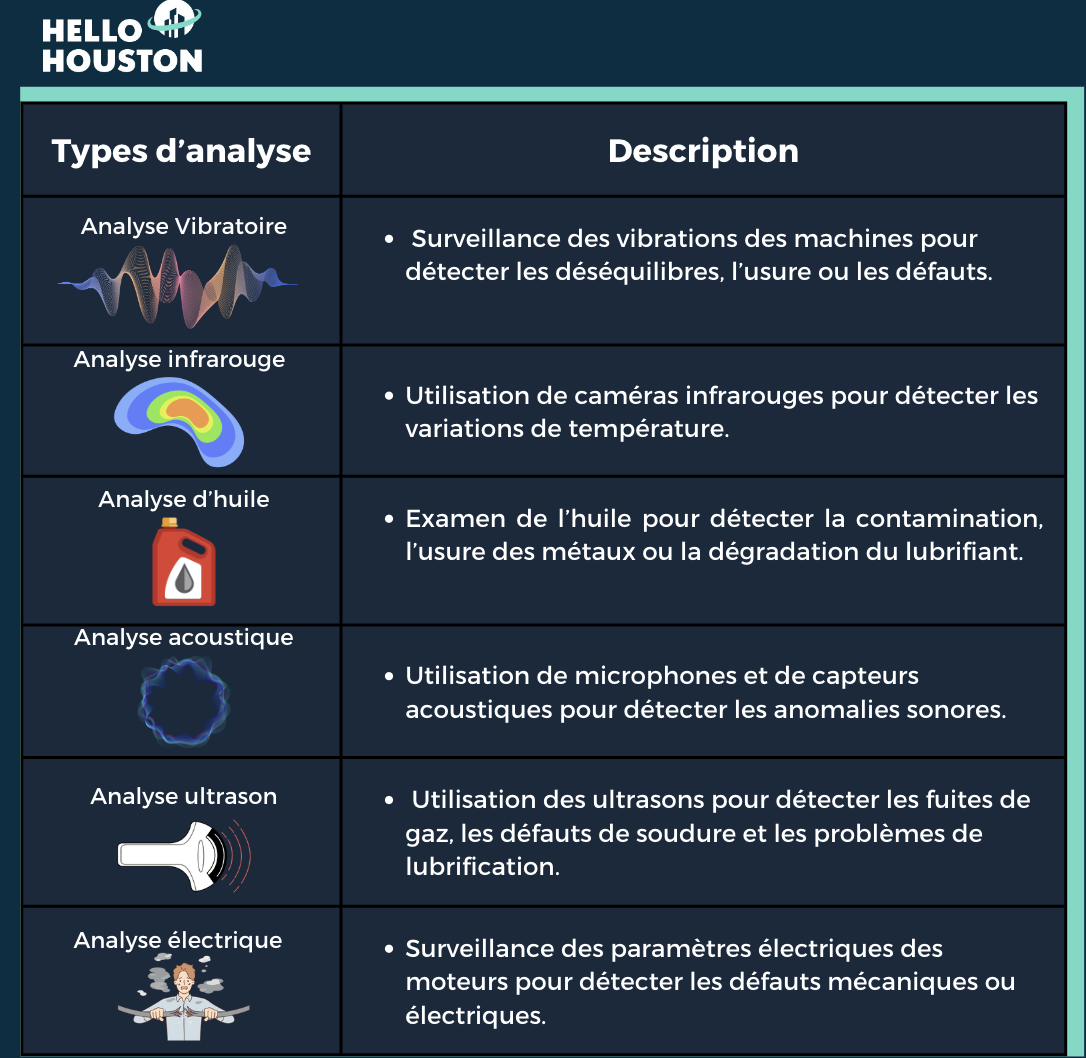
Why condition monitoring?
Conditional maintenance offers a number of advantages. It optimizes costs by intervening only when sensors signal a need to do so, thus reducing spare parts expenditure and saving resources. What's more, this method reduces stress thanks to continuous asset monitoring.
It also minimizes unplanned downtime, thanks to regular machine monitoring by technicians, who can detect signs of failure early and intervene in good time. This improves equipment reliability and ensures availability and continuity of production.
Finally, it prolongs machine life by ensuring rapid repair of operating problems, thus avoiding excessive wear and tear on mechanical parts and premature failure of other assets.
What's the difference between condition-based and predictive maintenance?
You've probably heard the expression "I do predictive maintenance".
It's "forecasting" rather than "predictive", which is a misnomer. But that's not today's topic.
Conditional maintenance is often mistakenly confused with predictive maintenance. However, these two strategies are, in a way, complementary.
Conditional maintenance
recovered during equipment operation and manufacturer information. Interventions are therefore carried out subject to conditions and thresholds that do not change as the equipment deteriorates.
Predictive maintenance
This is a more advanced version that uses IoT technology to analyze sensor data. It determines when tools will break down by tracking their degradation in real time. This method is more proactive, adapting to the life of the equipment, but is also more costly and complex to implement.
The choice between these two methods will depend on the specific needs of the company, its resources and the criticality of its equipment.
How to deploy condition-based maintenance in 6 steps?
If you want to implement condition-based maintenance, here are the steps to follow.
Step 1: Assessment of requirements and critical equipment
Use failure history to assess the criticality of equipment and identify those that have a significant impact on production.
Generally speaking, 20% of equipment can be responsible for 80% of breakdowns or associated costs (Pareto).
You then need to focus on the monitoring requirements (e.g. oil level, pressure, etc.) that your equipment will need.
Step 2: Selection of appropriate technologies
Select sensors adapted to critical parameters (oil level, pressure, temperature, vibration, electrical current).
Step 3: Data analysis and thresholds
Based on technical specifications, industry standards or your own experience, define anomaly reports.
Step 4: Determine the time that may elapse between malfunction detection and pre-failure intervention
Set alerts with a margin of maneuver to anticipate interventions before the equipment is in trouble, enabling efficient organization of technicians.
Step 5: Integration with existing systems (CMMS - HelloHouston)
Integrate monitoring and inspection data into HelloHouston to facilitate maintenance decision-making and automatically alert technical teams.
Step 6: Measuring the ROI of installations
Does implementing condition-based maintenance give you an excellent return on investment? To find out, compare maintenance costs, equipment lifetime, downtime, etc. This analysis should be carried out before and after system implementation.
Benefits of condition monitoring
Reduced breakdowns and corrective maintenance
Like any maintenance department, the ultimate goal is to never have to work at all. By proactively detecting potential breakdowns, technicians are able to act at the right moment, avoiding unscheduled stoppages that set the workshop on fire and blur communication with production teams.
No interruptions during production
High-quality products thanks to efficient machining tools
Longer-lasting, more reliable equipment
Enhanced safety
Well-maintained equipment is less likely to cause workplace accidents.
This contributes to a safer working environment and reduces the risk of injury to production workers and technicians.
Conclusion
I think you understand the benefits of this type of maintenance.
Conditional maintenance is the art of taking care of your machines at the right time. This saves on spare parts and reduces interruptions to production. And with HelloHouston's CMMS, everything becomes even easier: it centralizes data, schedules tasks and alerts you automatically.
If you'd like to talk to one of our engineers, contact us directly by clicking here!