Contents
Some CMMS features :
- Managing maintenance: preventive maintenance planning, corrective maintenance management, service requests (SR), work orders (WO).
- Inventory management: purchasing, rotation rate visualization, replenishment.
- Performance indicators: MTBF, MTTR, Pareto, preventive rate.
- Personnel management: scheduling, leave, skills, workload.
- Asset management : Location, documentation, condition.
Introduction
Maintenance management is what keeps all your company's equipment running smoothly.
Today, equipment that breaks down or malfunctions in the middle of production means lost profits. This can result in production delays, defective products, additional costs, etc.
The only way to avoid these disasters?
Improve maintenance management. All maintenance must be carried out on time, and all breakdowns anticipated. Technically, this is perfectly feasible. But only if you're prepared to invest significant resources and effort.
Unless you use a CMMS solution like HelloHouston.
This is maintenance tracking and planning software.
- What is it?
- How does it work?
- How can this new technology improve maintenance management?
Let's have a look around.
1- What is a CMMS?
In simple terms, CMMS is a software package that enables you to manage your maintenance efficiently, thereby increasing the reliability and productivity of your equipment.
It was created in the 1980s to meet two main objectives:
Manage and automate various maintenance operations.
How?
Thanks to its functions, which enable you to draw up a list of each piece of equipment to be serviced, or of their maintenance requirements, you can reduce the costs associated with unplanned shutdowns or last-minute repairs.
.webp)
How important is it for a company?
Maintenance management is above all a matter of anticipation.
Today, many companies use Excel.
But planning the various maintenance operations down to the last detail with a spreadsheet is both time-consuming and complex.
- Which team will be in charge of repairs over a given period?
- Spare parts for servicing a particular machine? Are they available in stock?
- When does equipment need cleaning?
That's a lot of details to sort out and control. And on a simple Excel sheet, the risk of error is high (breakdowns and malfunctions are hard to avoid).
The main advantage of CMMS is that it helps you to plan all your maintenance requirements automatically. This includes everything directly or indirectly related to maintenance (personnel, stock, cleaning, repairs, etc.).
Which sectors are concerned by CMMS?
As long as you have daily maintenance activities, CMMS is the right tool for you, and will save you time.
It is suitable for all sectors, whether industrial or :
- Real estate
- Transportation
- The medical field
2- Key CMMS functions
Even before its functionalities, a good CMMS can be recognized by its simple, user-friendly interface, which will naturally increase the efficiency of your teams.
A. CMMS for preventive maintenance planning
Preventive maintenance covers all operations that help to keep machines in good working order by carrying out servicing before they break down. The opposite of curative maintenance.
It serves two purposes:
- Extend equipment life and reliability
- Optimize productivity.
To plan and schedule these operations, CMMS allows you to :
1. Determine perimeter
2. Choose the type of maintenance (systematic, conditional...)
3. Choose maintenance frequency
4. Choose who will carry out the maintenance
Once all these details have been taken care of, the tool helps you to plan, execute and supervise all interventions.
B. CMMS for tracking interventions
Intervention management means organizing and coordinating maintenance operations in response to requests for intervention.
The idea here is to focus on added value.
For example, with HelloHouston you can :
- Manage human resources : the tool provides an overview of internal and external resources, as well as intervention times. This makes it possible to plan maintenance operations efficiently and on schedule.
- Reduce intervention times: the tool offers an easy-to-use interface with centralized information. Technicians have access to troubleshooting guides and equipment history (on a PC or Smartphone).
- Centralize service requests: everything is in one place, which will boost team productivity.
.png)
C. Computer-aided maintenance to monitor equipment
On a CMMS solution, you can consult the equipment inventory (list, model number, serial number, location, etc.).
It also provides user manuals, maintenance procedures, performance data, etc...
You can also view the history of interventions.
D. CMMS for purchasing and spare parts inventory management
This software also offers the possibility of managing purchases via purchase requisitions and spare parts inventories.
This is an essential function to avoid stock depletion and overstocking, which will help reduce costs.
How can HelloHouston help you manage your purchases?
By having access to the in/out traceability of each item. This means that the movement of each item is closely tracked (from order to delivery to use).
But that's not all: purchase requisitions are easy to submit, and that's a real time-saver when you consider how time-consuming it can be.
E. Reports and analyses
A functional CMMS comes with an intuitive dashboard, providing a real-time view of the status of the machine fleet. This is essential for rapid, factual and efficient decision-making.
These focus mainly on performance indicators (Maintenance KPIs)
The most common metrics include :
- MTBF: Mean Time Between Failures,
- MTTR: mean time to restart, repair, resolution or response,
- MTTF: Mean Time Between Failure,
- Preventive maintenance rate: rate of effectiveness of the preventive maintenance strategy,
- Number of operations to be planned
- Number of interventions started or treated
- Number of late interventions
- Budget used vs. planned
These maintenance indicators, or KPIs, enable us to determine how often incidents occur, and help us to define how quickly our teams can intervene.
It is thanks to this reporting that rapid decisions can be taken to make operations more efficient.
So a clear dashboard is essential.
.png)
F. Shift and task management
With Computerized Maintenance Management software, the manager has access to several key items of information.
- An overview of all teams (internal and external): data includes skills, their availability, authorizations, external resources with contacts...
- Planning of work orders: work order information is easy to consult and create.
This information enables efficient problem solving, thanks to the detailed and precise information provided by the ticketing system we offer.
In simple terms, the manager can monitor the performance of each technician in real time. He can also check the status of maintenance operations in real time.
G. ERP integration
data and facilitate information sharing. In fact, it's essential. Once connected, these two software programs form a kind of dataHub.
We absolutely want everything to be connected. So when you deploy HelloHouston you don't have to reconfigure everything.
Interfacing between the software and your ERP means that everything is at your fingertips, in the blink of an eye (inventory, purchase requisitions, HR, accounting, etc.).
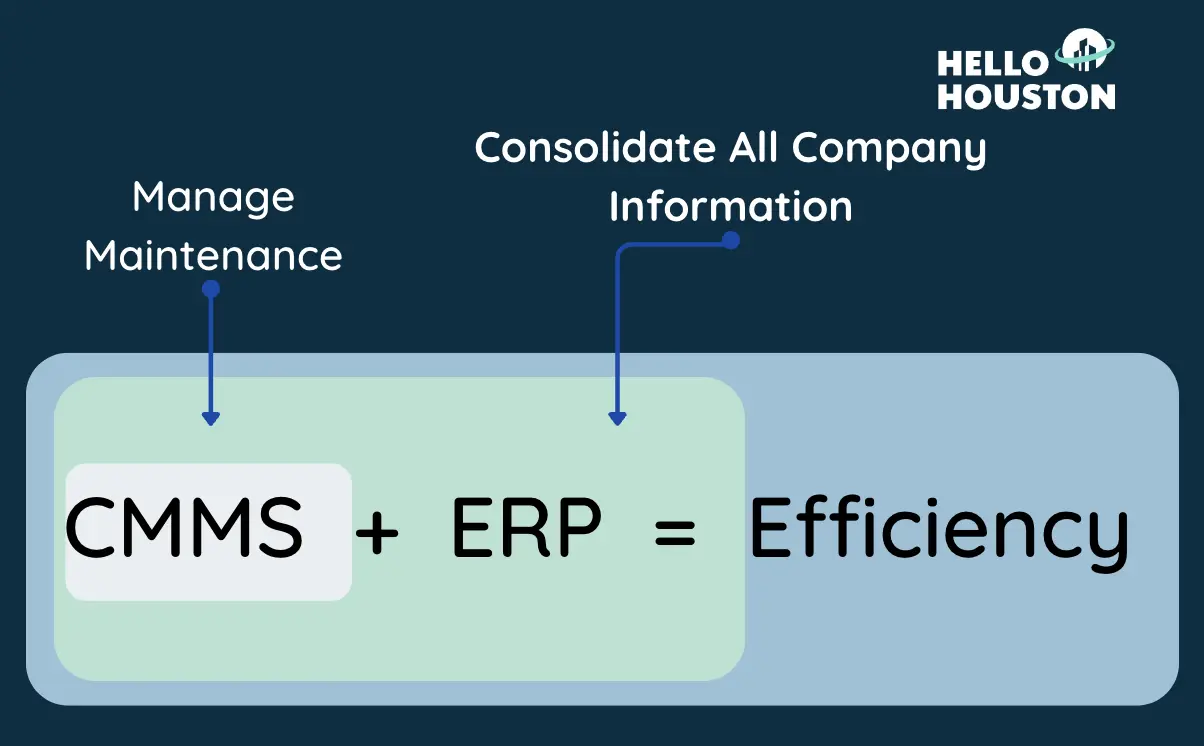
3- The benefits of using a CMMS solution
We've talked about functionalities, but what's in it for your plant?
CMMS to reduce maintenance costs
- Reduced corrective maintenance
- Inventory optimization
- Group purchasing
CMMS to increase equipment service life and reliability
Each machine isrigorously monitored.
Equipment interventions are well-targeted, which increases their lifespan. But that's not all: risks of malfunction can be easily avoided.
CMMS to improve operational efficiency
Resources are used efficiently.
Nothing is left to chance, and everything is optimized: response times, stock, human resources, response costs, equipment reliability, etc.
Technicians concentrate on adding value, not filling in Excel spreadsheets. Reports can be completed directly on the spot.
4- How do I choose the right CMMS software?
Choosing the right Computerized Maintenance Management System (CMMS) software is no easy task. You need to select a tool that not only meets your current needs, but is also scalable to adapt to future changes in your business.
- SMEs will prefer a simple, flexible CMMS.
- Larger companies, on the other hand, require a more robust and comprehensive solution to meet their needs.
A. Features
The software must be adapted to the type of equipment or machinery in your company's sector.
Before making your choice, compare existing CMMS solutions. Also check out the customization options.
B. Ease of use
Not all your staff are familiar with new technologies.
For this reason, a simple, intuitive interface is essential for easy integration.
It must be easy to use and understand for the majority of your teams.
C. Customer support
CMMS software is basically designed to facilitate the work of the maintenance manager. But if the tool encounters a problem, the editor must intervene quickly.
This helps to limit possible interruptions. That's why you need to choose a serious, reliable company with responsive customer support.
Be sure to :
- Support availability.
- Support channels (telephone, email, live chat).
D. Connectivity
Make sure the software can be connected to the tools you're using.
To do this, check for native connectors. These extensions will enable you to associate it with other tools.
With HelloHouston, you can connect the software with ERP or IoT.
5- How to deploy a CMMS
While CMMS can simplify and optimize maintenance management, it's implementation that often poses problems. Without the right methodology, implementing this tool can end in failure.
To ensure the success of your project, here are a few points to consider.
A. Assess management needs and objectives
You need to take into account a number of parameters such as: management requirements, objectives to be achieved, weak points, adaptation of the CMMS to the specific needs of your sector of activity...
What do I need?
Why do we want to deploy a CMMS?
How soon do I want to deploy it?
Who will be the project leader?
B. Implementation
Integration includes: data migration and integration. Data must be extracted in formats compatible with the CMMS solution of your choice.
This data must then be examined for standardization (validating the veracity or integrity of the information, removing duplicates, correcting errors, etc.).
They are then imported. The CMMS can then be combined with other tools.
C. Configuration and customization
This stage is essential to the success of the implementation. It involves
- Define maintenance schedules: to establish work order triggers.
- Establish model work orders: including data on equipment or machinery, operations to be carried out, etc.
- Set up monitoring parameters: equipment concerned, location, criticality, maintenance data, etc.
- Access levels: role-based access controls allow agents to access only the information they need to do their job.
- Customization also takes into account other details such as sector- or industry-specific standards, and much more besides.
D. Training and change management
To successfully integrate this new tool, users need to receive appropriate training.
This applies equally to managers, administrators, technicians and supervisors.
Training must include :
- tool operation,
- how to use it,
- methods for exploiting it to its full potential.
To help people embrace change with ease, you need to help them understand how this tool can make their work easier.
In the event of reluctance, reassure teams and involve them in the decision-making process.
Conclusion
In short, CMMS :
- Better anticipation of maintenance needs
- Reduces the risk of breakdowns and malfunctions
- Improves operational efficiency
- Minimizes costs
Does your company need this technology? HelloHouston offers a complete and intuitive CMMS solution.
We invite you to discover how our software can revolutionize your maintenance management.
Try HelloHouston today and see the difference for yourself.
For a demonstration or to find out more, contact us and take control of your maintenance.
FAQ - Answers to the most frequently asked questions about CMMS
Do you have questions about Computerized Maintenance Management Systems (CMMS)?
You're not alone. Here are some brief answers to questions frequently raised by professionals interested in this technology:
What is CMMS?
CMMS, or Computerized Maintenance Management System, is an IT system designed to optimize a company's maintenance strategy. It enables the planning, monitoring and analysis of all activities linked to the maintenance of equipment and infrastructures. By integrating valuable data such as user manuals, service history and stock levels, it becomes an essential resource for guaranteeing the efficiency and safety of maintenance operations.
What are the advantages of CMMS?
The benefits of a CMMS are numerous: improved productivity through reduced downtime, optimized inventory management, rigorous tracking of maintenance costs, extended equipment life thanks to effective preventive maintenance, and, last but not least, better compliance with safety standards and regulations.
How to choose your CMMS software?
Choosing the right CMMS software means taking a number of criteria into account: ease of use, ability to customize to the specific needs of each structure, ability to integrate existing data without difficulty, total cost of the solution (purchase or subscription, training, maintenance), and quality of customer support offered by the supplier.
How do you say CMMS in English?
Computerized Maintenance Management System